How to avoid bottlenecks in the fulfilment and distribution process.
According to Wikipedia ‘a bottleneck is one process in a chain of processes, such that its limited capacity reduces the capacity of the whole chain …’ In the fulfilment and distribution process bottlenecks can occur for a variety of reasons including inadequate equipment, inefficient processes or poor productivity.
Whatever the reason for it, a bottleneck is the slowest part of the process and therefore defines the rate of throughput, productivity and profitability of the entire operation.
First find your bottleneck
Before embarking on rectification, identifying the problem area is the first challenge. The pinch point can be an obvious one: a particular stage where input is arriving much faster than the following process in the line can handle it, slowing output down. This can be caused by an inadequate use of manpower, insufficient equipment or technology, an unsatisfactory warehouse layout or inefficient processes.
If the cause isn’t an obvious one, data can be used to decipher where the bottleneck problem is occurring. A sophisticated warehouse control system can not only collect useful data but can also provide high-level analytical insights into each aspect of warehouse performance to highlight bottlenecks.
Automate to eliminate bottlenecks
Reducing labour-intensive manual operations in a pick, pack, sortation and dispatch operation and replacing them with a materials handling automated system can transform productivity and prevent chokepoints.
One guaranteed way to improve processing speed and accuracy is to install a sortation system. There are various different sorters available depending on the product to be processed and the available space within a facility.
To ensure that you receive considered advice on which sorter would be most suitable for your facility, call Axiom and discuss with our sales and design engineers your specific requirements. Axiom has gained a reputation for providing automated systems that meet the high standards required in today’s fast moving warehouse facilities.
The Lynas Foodservice Group, one of Ireland’s largest food distributors, called on Axiom to help when they were experiencing a bottleneck in their operation.
As a result Axiom installed an innovative sortation system in the new Lynas distribution hub located in Lusk, County Dublin. The sortation system is capable of sorting 45 diverse food products a minute to 11 destination lanes.
This has enabled the Lynas facility to process up to 20,000 products in a single shift. For more information, head to our Lynas Case Study and see a video of the sorter in action.
A reliable conveyor system to boost productivity
One vital link in the processing chain is a reliable conveyor system. Most automated processes still depend on smooth running conveyors to feed products down the line to a sortation system. As a consequence, any malfunction in the conveyor system can rapidly cause downtime and an inevitable bottleneck.
Most modern conveyors are made from high quality materials and can be relied on to run consistently 24/7. They can now be built with the added advantage of a zero-line pressure (ZLP) accumulation capability.
With ZLP, the conveyor is split along its length into individually controlled zones. Inbuilt sensors feed information to the control system regarding whether a zone is occupied or free. The ZLP system ensures that a product doesn’t come into contact with another product and automatically detects when there is sufficient space to allow product to go down the line.
Operating this way means that any hold-ups do not result in a chokepoint which could mean the whole line shutting down. The result is an extremely productive system.
Taking preventative measures – training and maintenance
Although a pick, pack and dispatch facility may be heavily reliant on technology, there will still be processes that depend on human involvement. A well-trained and motivated workforce with access to the right tools is a win-win situation within any warehouse. It is essential therefore that the workforce can operate efficiently and that there are sufficient hands-on-deck to avoid potential problems that could lead to bottlenecks.
Keeping machinery and equipment serviced and well-maintained is an important factor to help prevent breakdowns. To assist with this, many companies with automated facilities take out support and maintenance packages. These can be tailored to individual requirements and budgets and are specifically designed to prevent the occurrence of damaging stoppages.
Act now to prevent bottlenecks
Any constraints on productivity impact on a company’s ability to achieve peak performance and profitability. There’s no doubt, therefore, that identifying and fixing bottlenecks will improve the overall productivity of a business. However, taking positive steps now to avoid bottlenecks altogether will prevent the pressure and problems they inevitably place on any busy facility with deadlines to meet.
Why Axiom GB Ltd?
Axiom are a family business based in Tamworth, Staffordshire, UK. The company has 25-years of experience as a leading supplier of material handling automation solutions across a range of industries, but specialising in the supply of systems for logistics, warehousing and fulfilment applications. The combination of conveyors, sorting systems, control and data handling provides turnkey projects for many well-known companies.
By reviewing each project on its own merits, Axiom strives to provide the optimum solution to exceed the base requirements of the automation.
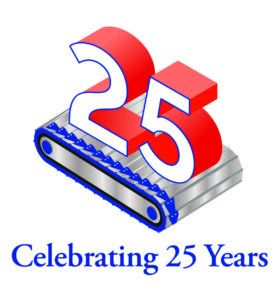
Join Axiom in celebrating 25-years in business. Keep a watch out for news items and regular updates for an exciting year.
Let’s talk….
We’d love to help you solve your materials handling challenges.
Contact Us
+44(0)1827 61212